Defining and contextualising track and trace in logistics
In simple terms, track and trace determines the current and past locations of objects (such as raw materials, products and vehicles) or people.
It creates visibility, traceability and resiliency throughout a supply chain, and allows goods to pass from point-to-point securely.
This is achieved through scanning unique barcodes – creating an audit trail of its journey as it passes through the supply chain.
This audit trail helps businesses to:
- Quickly understand what certain items, packages or cargoes are
- Find where items are located across the supply chain
- See where and when items have been handled or delivered
- Know who handled them and at which points.
All of these points are of particular importance to businesses working in highly regulated sectors where there are legal traceability requirements, such as pharmaceuticals or food, which rely on transparent supply chains to function.
There are a number of benefits that effective track and trace brings to a supply chain, including:
- Saving time and reducing costs
- Improving security and resilience
- Streamlining workflows & optimising operations
- Boosting customer satisfaction & reducing customer support
- Helping to identify bottlenecks in the supply chain
- Eliminating the use of spreadsheets.
We will contextualise these benefits through a variety of examples relating to specific industries and scenarios to help better understand how businesses use track and trace, and where it is most effective.
Track and trace in the food industry: No more horsing around
As alluded to in the introduction, the food industry is highly regulated due to the nature of the products, so there are stringent laws and litigations that have to be followed in order to protect the end consumer and those who are handling the food across the supply chain.
The EC Regulation 178/2002, for example, sets the general principles and requirements of food law and lays down procedures in matters of food safety. The legal document includes a dedicated Article to traceability: Article 18, which states:
“The traceability of food, feed, food-producing animals, and any other substance intended to be, or expected to be, incorporated into a food or feed shall be established at all stages of production, processing and distribution.”
Due to the advancement of smart technologies such as ePOD software and handheld rugged devices, the traceability of food has never been more secure, accurate and accessible across the whole supply chain.
Supermarkets trace food products through global trade item numbers, which allow data to be collected and recorded, such as the manufacturing date, place of origin, item type and expiration date.
This is paired with a companion system of global location numbers, which pinpoint each geographic stage in the process, starting at the production source, such as a farm, all the way through to the supermarket.
The technology highlights any potential vulnerabilities and reduces the risk of food fraud before it reaches their shelves and the consumer.
Many will remember Horsegate, also referred to as the 2013 Horsemeat Scandal, when horse meat entered the food supply chain as beef, and ended up being sold in many products in the UK.
Testing revealed beef products had been adulterated with horsemeat such that horse DNA was identified in 37% of beef burgers purchased from food retail stores including Tesco, Dunnes, Lidl and Aldi.
It resulted in millions of product withdrawals, huge financial losses, and consumers being unknowing victims of food crime.
More stringent laws, in tandem with efficient track and trace systems, now help to safeguard against such errors occurring at scale in future, as products can be quickly located, identified and removed from circulation.
Track and trace in retail: Helping businesses to deliver
From inventory management to last-mile delivery, track and trace has permeated retail in a variety of ways – all of which have contributed to helping businesses meet ever-growing consumer expectations surrounding last-mile delivery, such as increased transparency, speed and reliability.
Customers more than ever want to know in precise detail:
- Where their package and delivery driver is through real-time tracking
- What time their order will be delivered
- The various options available to them if they’re not in to receive it
Delivery day has become an integral part of a customer’s experience with a brand – a poor delivery experience can not only tarnish a company’s reputation in the eyes of the consumer, but it can hurt their revenue too.
57% of consumers said that they would avoid using a retailer again if they had a negative delivery experience.
Real-time delivery tracking information for customers has become integral to delivery day – offering customers the ability to track their orders in real-time and give them full visibility as to the precise location of their delivery.
This reduces the chances of failed deliveries as the customer knows when to expect their delivery, saving both time and money that would be otherwise wasted on re-delivery.
Customers increasingly expect deliveries to be fulfilled within one to three days of ordering for most products.
Track and trace has revolutionised the speed and reliability of inventory product picking to make fast delivery times a reality.
Smart technology such as radio frequency identification (RFID), which has a higher accuracy and speed rate in comparison to barcode scanning, assists employees in quickly locating items to increase in the shipping and picking accuracy, as well as the overall output of the employees.
Inventory tracking which utilises real-time data eliminates the need for manual inventory counts and allows businesses to monitor product storage space so that they can save on warehousing and storage costs.
Whether it’s at the beginning of the supply chain or the end, track and trace continues to be utilised in clever ways, but before any technology is implemented, retailers have to have a clear understanding of their supply chain.
Each chain comes with their own processes and complexities that vary from retailer to retailer, so they need to know the ins and outs of all the processes involved, such as how it functions and the individuals responsible for ensuring it does.
System Integration Expert and Managing Director of Outserve, Philip Oakley, alludes to this and offers advice to retailers who are looking (or may be struggling) to implement track and trace effectively:
“Although we would have lots of advice we would say that the number one piece of advice would be to start with ‘people and process’ before ‘software and systems’. Map out how your items physically move in and out of the business from the very beginning to the very end of the process. Then you can think about how the traceability needs to work, at what points you need to record it, where it may change, and where it will end. Also, give significant consideration to your reporting requirements. Who will need traceability information, when will they need it and in what format will they need it in.”
COVID-19 highlights the importance of track and trace technology on a mass scale
Track and trace, its concepts and premise in particular have all gained significant traction since the onset of the COVID-19 pandemic, albeit in a slightly nuanced form to the traditional tracking and tracing previously alluded to.
The foundations of the NHS COVID-19 ‘Test and Trace’ application were simple – it was a contact tracing application that used a combination of Bluetooth technology and QR code scanning to determine hotspots of the virus, and alert those that had downloaded the application if they had been in contact with someone who recently tested positive for COVID.
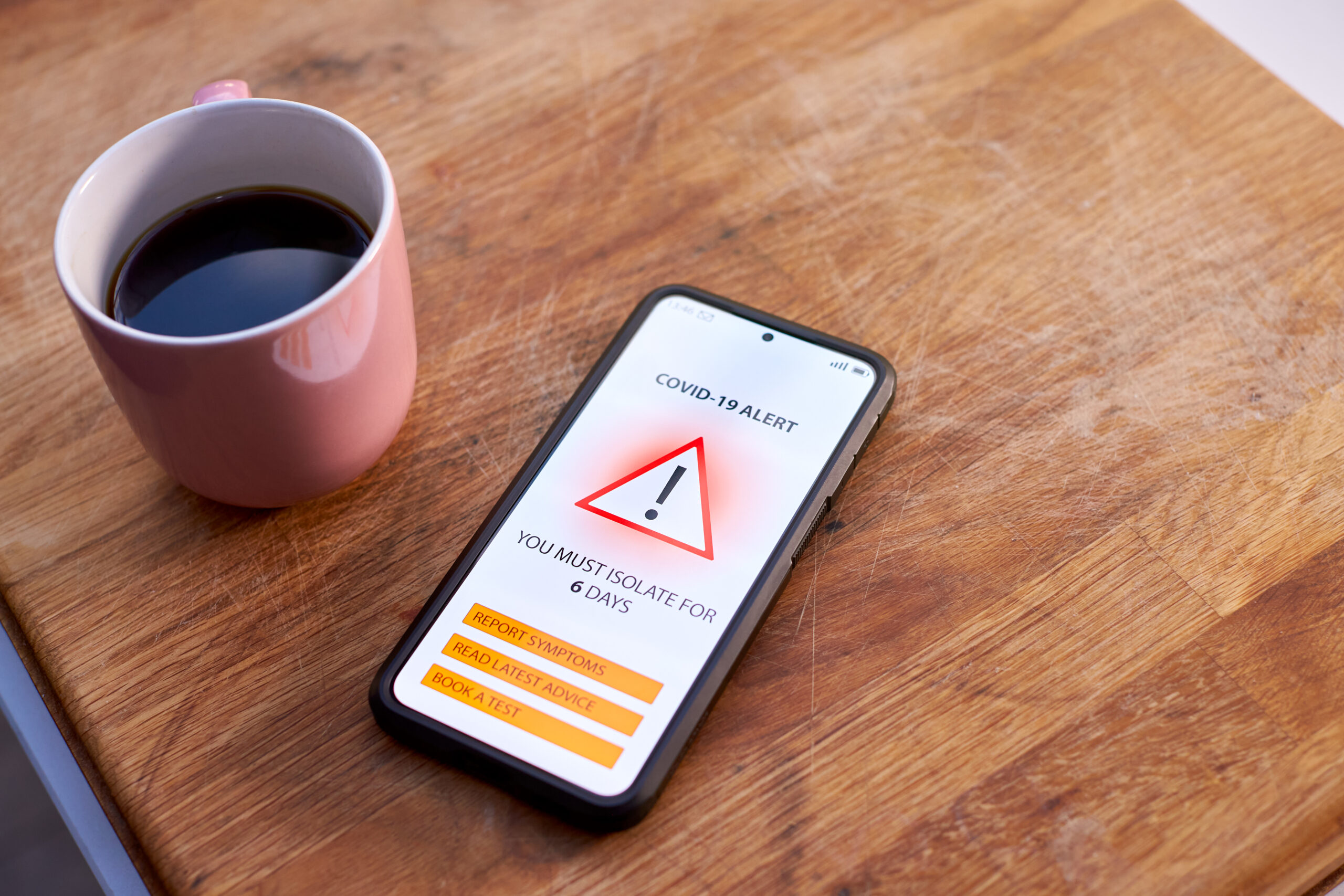
It ultimately helped to identify places where infection would be likely, helping to play a pivotal role in controlling the reproduction rate of the virus in order to save lives.
The pandemic highlighted on a global scale the importance of real-time tracking, as well as the role it can play in creating end-to-end transparency on a mass scale.
The NHS ‘Test and Trace’ application redefined for many what track and trace involves outside of giving an end consumer visibility over their order from ASOS.
The pandemic caused unprecedented disruption to every entity of the supply chain and none more so than manufacturers.
Logistics decision makers came to the realisation that their supply chains lacked true end-to-end visibility, and the resiliency it brings to help them cope with disruption on this magnitude. Now companies are utilising smart track and trace technologies more than ever in order to reduce risk and cut costs, as real-time data enables them to make more informed decisions on performance, such as how efficiently they move goods and the impact this has on the end consumer.
How track and trace is transforming the pharmaceutical supply chain
An intensified focus on healthcare, precipitated by the COVID-19 pandemic, and an ever-shifting regulatory environment has accelerated the need for increased transparency across the full pharmaceutical supply chain – from raw materials to last-mile patient delivery.
Technology holds the key to safeguarding these chains against new regulations from governments, industry agencies and future disruptions, as it allows the various entities within the supply chain to shift to more predictive and responsive operations; and set stronger foundations from which supply chain resiliency can be built upon.
As a consequence, investment in track and trace technologies to provide end-to-end visibility, streamline operations and achieve compliance is currently rife within the industry.
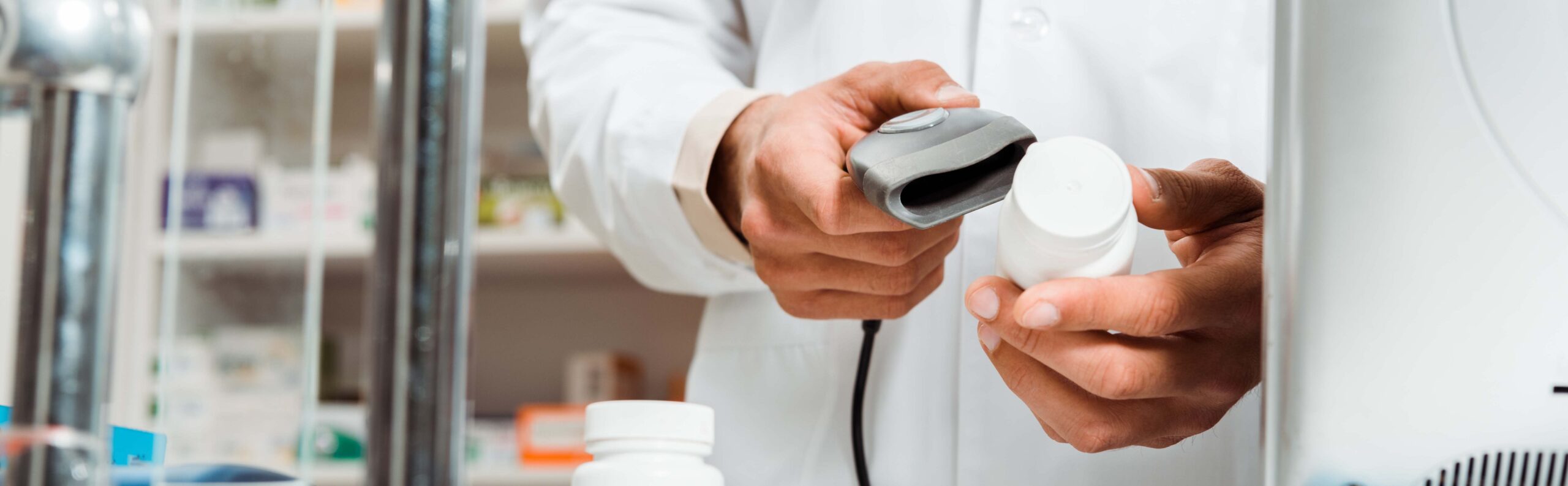
Pharmaceutical enterprises believe that by enhancing the track and trace capabilities of their devices and software it will improve productivity, add invaluable visibility to the supply chain, and provide greater security to future-proof operations.
Track and trace technology has evolved to provide pharmaceutical practices and logistic companies with a wealth of benefits on a day-to-day basis, such as:
- The ability to detect and respond to risk posed by counterfeit or substandard products
- Increased patient safety from compromised medications and other products
- Improved team productivity and workflow conformity
- Increased product/asset visibility and utilisation
- Enabled informed real-time decision-making and regulatory compliance
All of which have the wider effect of improving medication quality and efficacy. Through stringent tracking and tracing the likelihood of improper storage that relates principally to erroneous refrigeration and temperature control is heavily reduced. It also minimises the risk of illness and possible death due to contaminated, tainted, falsified or counterfeit medications making their way into the supply chain, as they are flagged upon scanning and can be withdrawn accordingly.
There are a number of advanced technologies that have been developed and implemented in order for supply chain entities to transition from reactive to predictive operations:
- Temperature-sensitive labels and item/batch level monitors
- Location technology
- Temperature monitors and sensors
- Mobile barcode labels and thermal printers
- Rugged scanners and the Internet of Things (IoT) and artificial intelligence (AI) technologies
Frequently Asked Questions
Track and trace determines the current and past locations of objects (such as raw materials, products and vehicles) or people. It is most widely used and associated with helping businesses and customers monitor the progress of last-mile deliveries.