Technology has long been a driving force for improving warehouse productivity, and that isn’t something that’s about to change.
For years, warehouse operations have been evolving to adapt to:
- Changes in consumer behaviour
- Productivity challenges
- Recruitment & labour
- Increasingly interconnected supply chains
In the recent Warehouse Vision Study: Dynamic Markets Demand Warehouse Agility whitepaper, mobile handheld computer manufacturers Zebra identified that 87% of warehousing decision makers have confirmed the need to implement new technology to stay competitive in the current on-demand economy.
So let’s dive into some of the challenges warehouse operators have been facing and how they’re using technology to remain competitive.
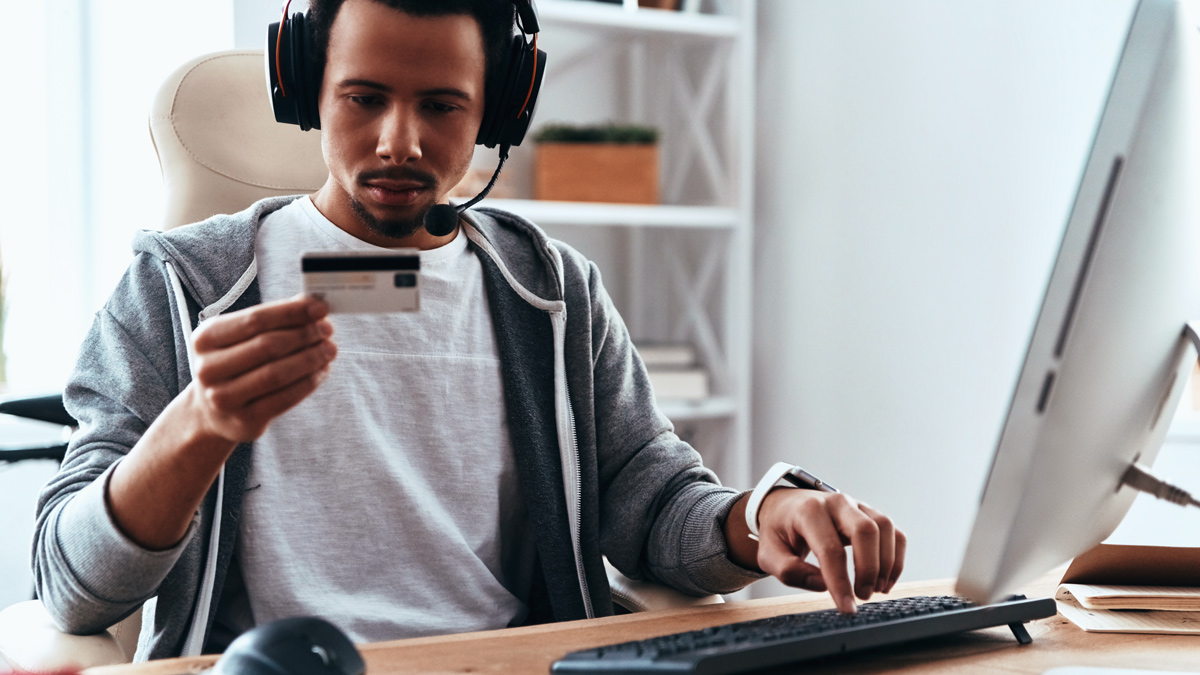
Changing consumer behaviours affecting warehouse productivity
Throughout the digital age, consumer behaviour is something that has been changing rapidly.
We’ve gone from having to leave our homes, visit the shops and make our purchases, to being able to buy products showcased by our favourite celebrities straight from Instagram.
Convenience is one of the big factors when it comes to these behavioural changes, and that’s not just when it comes to actually purchasing our goods and services.
It also applies to how our goods get from the vendor and into our homes.
73% of shoppers said they prefer to have items delivered to them rather than picking them up.
And this change in behaviour has been greatly accelerated by the COVID 19 global pandemic.
With an increased number of people working from home, better prices offered online than in store and next-day delivery more widely available, consumers are prioritising convenience when it comes to making their buying decisions.
Retail decision makers have had to respond to this behavioural shift with an increased focus on optimising their e-commerce and order fulfilment operations to meet the growing demands of their customers.
80% of retailers said they are under high pressure to offer a variety of delivery options and speeds
Jordan Westley, ecommerce and order management system (OMS) expert at Mintsoft said:
“Choosing to opt for automated technology will allow fulfillment and warehousing businesses to be more efficient by using platform data to make more informed and calculated decisions – whether it be around inventory, returns processes or even selecting the best courier for the job.”
“With the competition of the ecommerce sector continuing to grow, it’s so crucial that you shine a spotlight on your order management and logistics software to keep your customers happy with a timely and efficient delivery.”
“Investing in an order management system with pre-built courier and multi-carrier API integration capabilities will allow you to simplify and speed up delivery times and the overall shipping process. Although it might take up more time to research and identify the best couriers to work with and set up relevant integrations, you’ll thank yourself in the long term by ensuring that items turn up on time, in condition, and with a delivery price that your business (and customers) can afford.”
“With rising fuel costs and a nationwide cost of living hike, offering a competitive delivery pricing will allow retailers to stand out from the competition – as will the ability to meet customer demands of choice, flexibility and speed.”
Consumers being able to order something online and have it delivered to their doorstep within 24 hours has increased the pressure on warehouse operators, as they have to grapple with order fulfilment, picking efficiency, order accuracy and outbound shipping operations.
And it’s technology that’s helping warehouse operators overcome these consumer-driven productivity challenges.
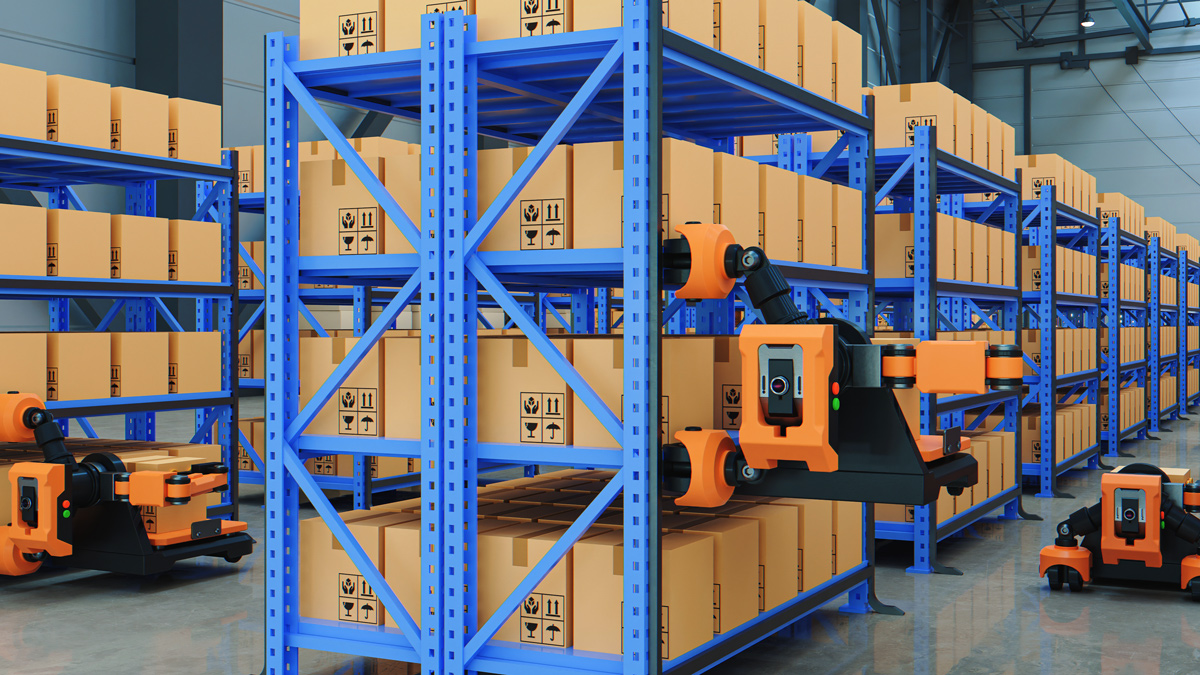
Technology assisting warehouse productivity challenges
It doesn’t matter whether you work in accounting, manufacturing or logistics, technology has been the key driving force behind increased productivity in just about every industry.
Efficiency is driven by being able to get more done in either the same or less time and that’s why technology has played a key role in warehousing.
Warehouse operators providing their workers with scanners and handheld devices has enabled a more efficient picking process as well as a reduction in the number of human errors that get made.
When this same survey was published by Zebra back in 2019, nearly a quarter (23%) of the respondents were managing their operations on paper or through fixed workstation systems. (Decision makers expect this number to fall to less than 5% within the next five years!)
Not only this, but by the information being fed straight back from the device into the enterprise system, warehouse operators are able to gain real-time visibility of inventory across their entire operation.
When we published a post last year on advice for retailers preparing for peak season shopping periods. Patrick Prasad (Head of Strategic Partnerships at Mintsoft) said:
“By monitoring inventory closely, eCommerce businesses will also be able to manage warehouse capacity more efficiently and implementing technology will help to support a more complex warehouse as a result of increased operations and allow you to scale up and down as needed.”
But now we’re seeing further advancements in warehousing, which includes the use of Autonomous Mobile Robots (AMR) to help lighten the workload of the frontline workers.
You would be forgiven for thinking that increasing the use of robots will decrease the need for workers, but in actual fact the robots operate as assistants, rather than replacements.
The AMRs help workers improve accuracy, save time on transporting goods to, from and between pick zones as well as reducing the physical burden on the workers.
And it’s not only the current workers that technology is having an impact on, but also the future warehousing workforce as well.
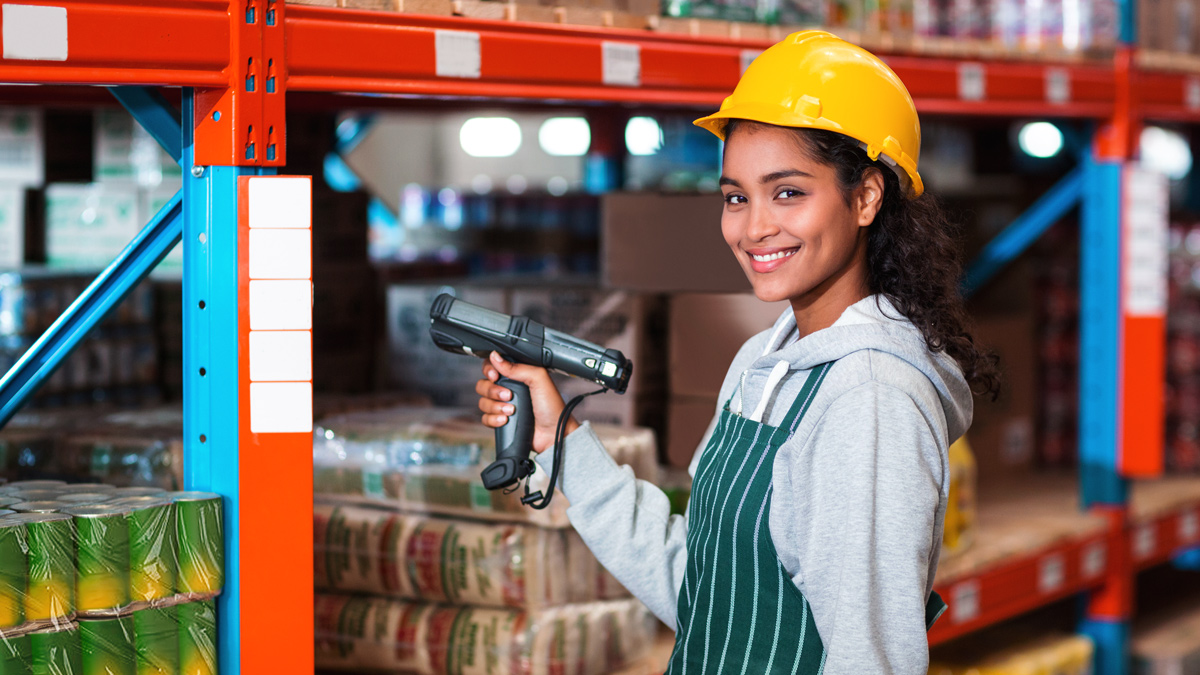
Impact of technology on the future warehouse workforce
The next generations of workers have been brought up in the digital age, having access to just about everything they need right in the palm of their hands.
So expecting them to enter a workplace where they then need to document the locations and movements of thousands of items every day seems like quite a big ask.
92% of workers agree that technology advancement will make the warehouse environment more attractive to workers.
That’s why it’s so important for warehouse operators to invest in technology for their warehouse, not just to remain competitive in the current market, but also to make sure their workplace is not alien to the future workers they’ll rely on to run their operation.
83% of workers said they would be more likely to work for an employer that gives their staff modern devices, versus one that provides older or no devices.
While many of the headlines recently have reported struggles for recruitment in warehousing and logistics, it’s actually had a positive impact, with 82% of staff saying their employers struggle to recruit has actually resulted in improvements, such as:
- Improved working conditions
- Use of technology to make work easier
- Increased wages and bonuses
- Technology enabling flexible work shifts
And the use of technology to make work easier goes back to our earlier point on efficiency, as its enabled warehouse workers to get more work done in either the same or less time.

Increasing visibility across interconnected supply chains
At any point in the supply chain where there is a breakdown of communication, whether that be between people or systems, it creates a black hole of information where nobody can be sure exactly what’s going on in that part of the process.
With supply chains becoming increasingly interconnected, it’s only through technology that we’re able to create end-to-end visibility for all network partners across the entire supply chain.
And that’s why warehouse operators are seeing this as a key point of investment for their business over the coming years.
54% of decision makers improvement plans, over the next 1-3 years, include investing in increased visibility across the supply chain.
For businesses involved as part of a global supply chain, that end-to-end visibility becomes increasingly important.
Remember when the Ever Given got stuck in the Suez Canal last year? Well that caused a major disruption to thousands of businesses, as not only was it carrying around 18,300 containers itself, but it blocked a major shipping lane for all other vessels transporting goods between continents.
For businesses operating without end-to-end visibility, this put a big question mark over where their orders were, when they would receive them and if in fact they would receive them at all.
Here at Stream, we’ve worked with some of the most widely used business and e-commerce platforms to build comprehensive integrations that help businesses gain end-to-end visibility across their supply chain.
Stream helps extend visibility from the moment an item is loaded onto a vehicle, right up until it arrives at it’s destination, whether that’s moving from one depot to another, or being delivered and signed for at the customer’s address.
Want to learn more about how Stream can help extend the visibility of your operation? Check out our pages on Route Planning & Route Optimisation, Electronic Proof of Delivery (ePOD) and Real Time Order & Delivery Tracking for your customers.
Download the full Whitepaper
Download the Dynamic Markets Demand Warehouse Agility from Zebra for more tips on strategic and operational insights to optimise and advance your operations, outpace your competition and increase your employee satisfaction.